Maketeam AR: Innovation in the creation of large-scale educational models.
MODELS OF THE CASTLE & AUGMENTED REALITY (AR).
WHAT IS THE OBJECTIVE OF THE MAKETEAM AR PROJECT?
The Maketeam AR project aims to create educational models of large French strongholds. These will highlight the sites on which they are located by bringing back to life structures destroyed over time, or by providing an overview of a castle several hundred meters long.
Once a model is completed, a layer of augmented reality, allowing the visualization of textures and paintings as they existed at the time, can be displayed through a smartphone or a tablet.
The project’s partners are the SUNI platform (École Normale Supérieure de Rennes), Maillard and Maillard company (stone cutting) and the Smart cooperative (augmented reality). The SUNI platform is responsible for creating a model production path (including material and process choice) and for creating a first large-scale demonstrator (a model of 2 x 1.5 meters).
Worldwide, many models represent the beauty or complexity of an architectural structure like the model of the Fougères castle in the Brittany region. In most of these cases, the models are made of metal, using a “metal mold casting” process. This process is costly and does not allow for very large models.
Here is the model of the Fougères castle and application of augmented reality in images:

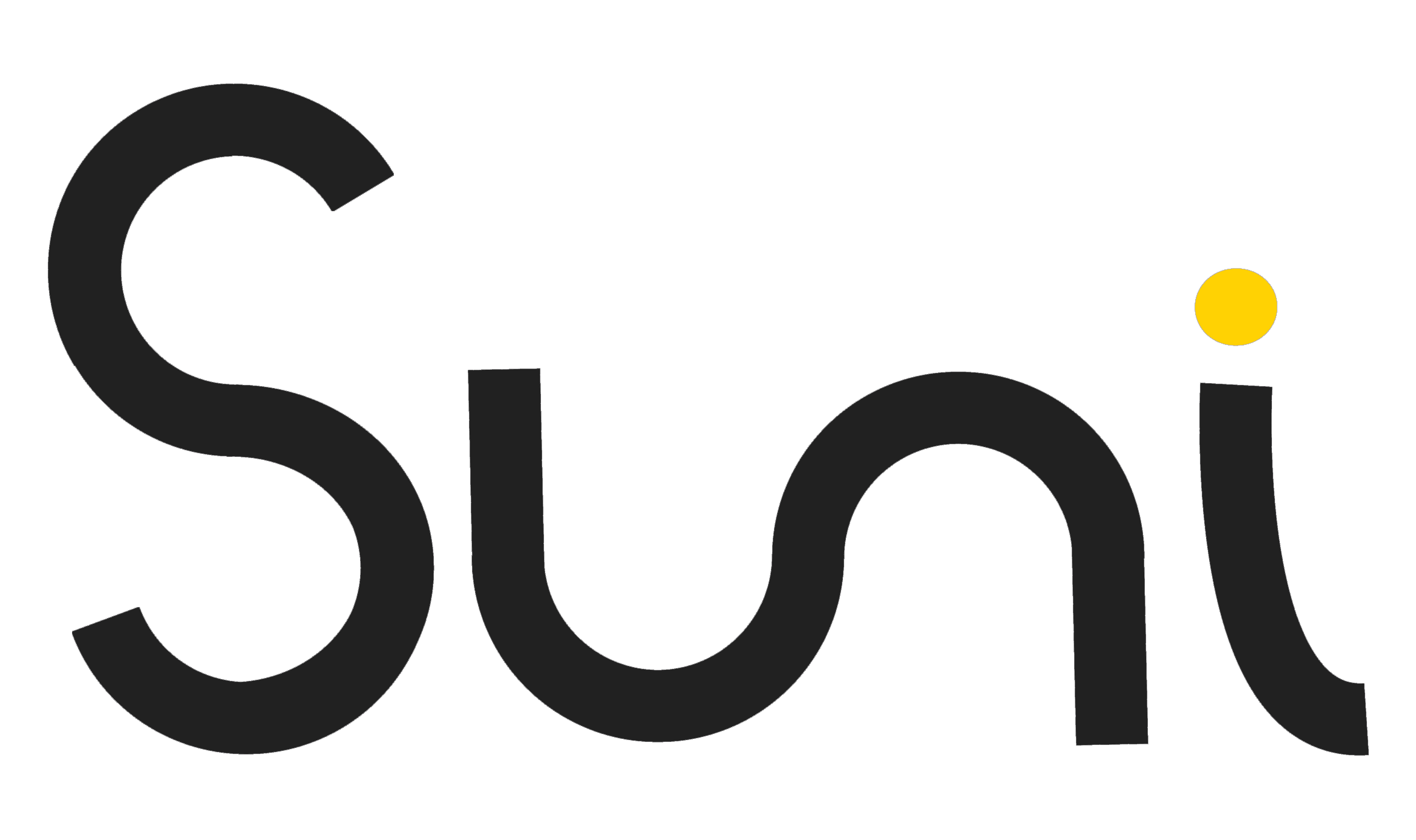
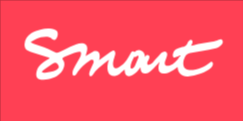
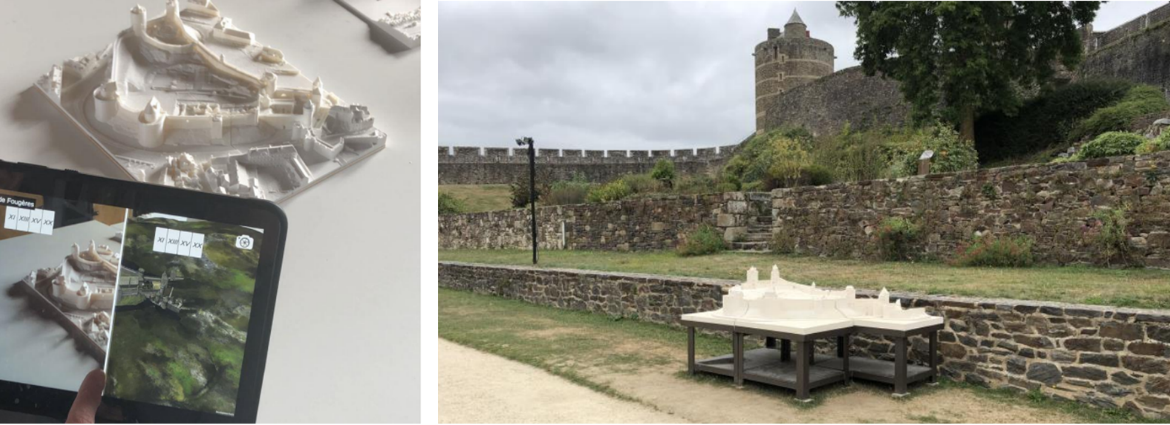
Application of augmented reality with a castle model
Model of the Fougères castle
SPECIFICATIONS OF THE MODELS CREATED WITHIN THE PROJECT
- The models will be stored outdoors and must therefore withstand weather conditions (rain, heat, marine environment, radiation, etc.). They must also be durable. The material used must therefore be chosen based on these elements;
- The models must have sufficient resolution to reveal the geometric details of the represented structures (stone effect on the walls, machicolations, windows, etc.). The chosen process must be adapted to this constraint;
- The models must be large (ground footprint over 1 square meter). The machines used must have sufficiently large workspaces to meet this constraint;
- Costs must be minimized to reduce the selling price of the models. They aim to be sold to small municipalities without large budgets.
WHAT MODEL TO CREATE AS A DEMONSTRATOR FOR THE PROJECT?
It was decided to create the model of the Guildo castle as it existed in the 15th century, as a project demonstrator (located in the municipality of Créhen in the Côtes d’Armor department, in France).
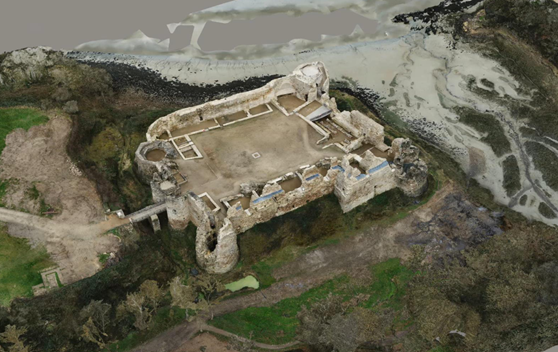
Valorization site of the Guildo castle
Indeed, it was during this era that the castle reached its peak, under the leadership of Françoise de Dinan, who carried out numerous improvement and beautification operations. At the end of the 15th century, the Franco-Breton war severely damaged the Guildo castle. A slow reconstruction of the castle began in the early 16th century, but the War of the League (1588–1598, opposing the Protestant King of France, Henri IV, to the Catholic troops of Duke de Mercœur) ruined the castle. The Guildo castle was abandoned in the early 17th century, cultivated, and used as a stone quarry until the early 20th century. In 2017, the Côtes d’Armor department allocated 2.7 million euros to enhance the castle ruins.
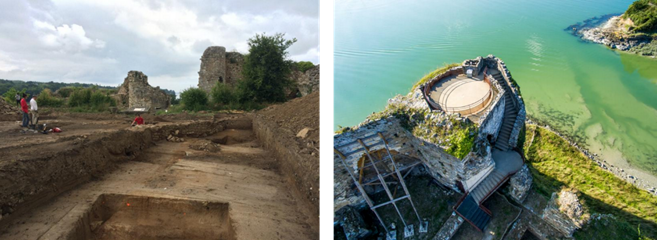
Archaeological excavations and valorization of the Guildo castle
The model to be created, illustrated by an artist’s view
- The castle’s structure, as it existed in the 15th century, was modeled based on historical documents. The geometries were validated by historians;
- The ground around the castle will be stratified to highlight the castle’s structure and improve the model’s readability;
- The ruins, as they exist today, were scanned and implemented in addition to the structure;
- Two accommodations, allowing the fixing of signposts for sighted and visually impaired people, were added.
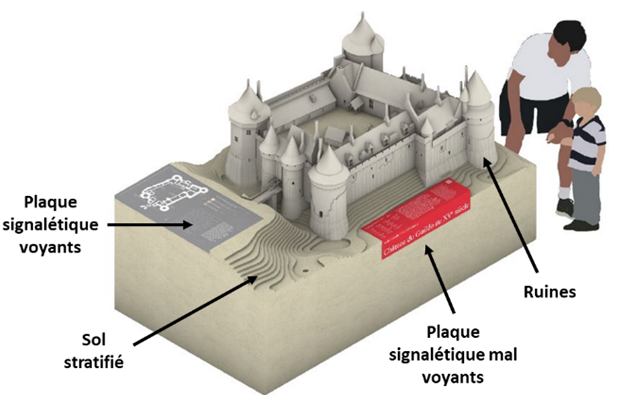
Artist’s view of the model to be created within the Maketeam project
TESTED AND ANALYZED MANUFACTURING PATHS
To create large models, several manufacturing paths were tested and analyzed. They are divided into two categories:
- Direct manufacturing paths: the model is created in a single operation (excluding finishing operations such as support removal or primer/paint application). This can be a material deposition operation (in the case of an additive process) or a material removal operation (in the case of machining);
- Indirect manufacturing paths: an indirect manufacturing path means that the model is created in more than one operation. This mostly includes molding processes and hybrid processes (for example, additive/subtractive).
- The following direct manufacturing paths were tested, through the realization of the demonstrator presented here: polymer powder sintering, stereolithography, 5-axis metal machining, 3D printing, and cellular concrete machining.
Voies de fabrication indirectes : une voie de fabrication indirecte signifie que la maquette est réalisée en plus d’une opération. On retrouve en majorité les procédés de moulage et les procédés hybrides (par exemple, additif / soustractif).
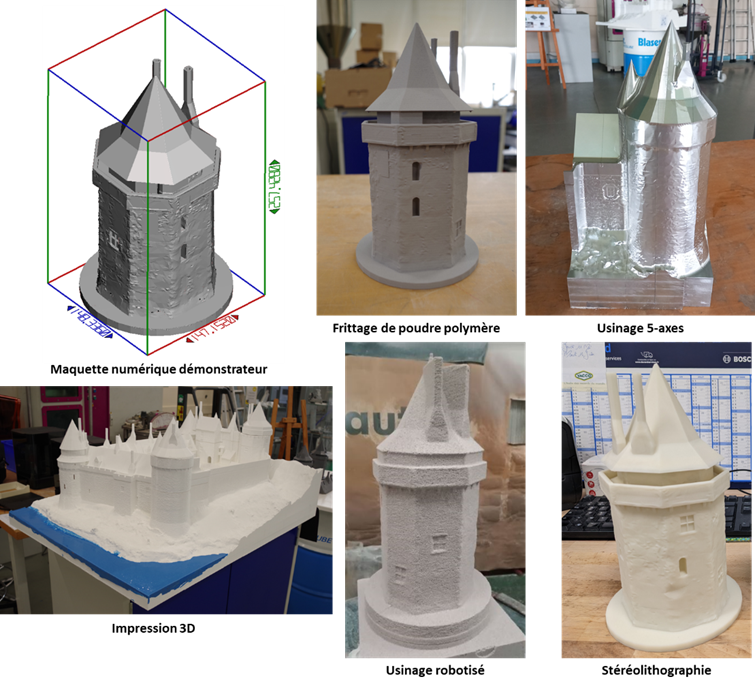
4 Direct manufacturing paths, demonstrators created
Unfortunately, none of the direct manufacturing paths were satisfactory. In some cases, the material used did not meet the specifications (stereolithography or 3D printing).
In other cases, the resolution was not sufficient (robotic machining), the manufacturing costs were too high (5-axis machining), or the process was not suitable for making very large parts (polymer powder sintering).
Indirect manufacturing paths were then considered. Some were immediately ruled out as too costly (metal molds, lost molds requiring the creation of a master model, silicone molding). Others were tested and analyzed:
- Molding in a semi-rigid 3D printed mold;
- Lost mold without master model: Mold created by the binder jetting on a sand bed process;
- Mold created in large-format 3D printing.
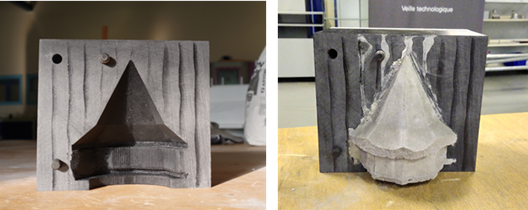
semi-rigid mold in 3D printing
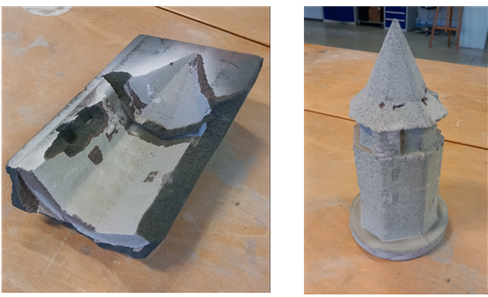
mold created by the binder jetting on a sand bed process
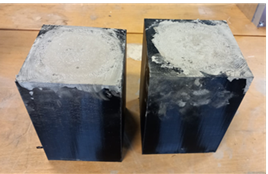
Validated manufacturing path – mold created in 3D printing
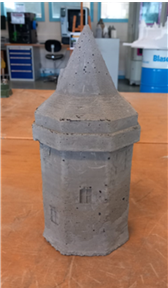
Conducted tests on the indirect manufacturing paths
The molding of a part of the roof of the Guildo castle, in a semi-rigid mold, was not conclusive, as the rigidity of the mold did not allow the demolding of the undercut geometries. The mold created by the “Binder Jetting on Sand Bed” process did not meet expectations in terms of resolution (the geometric details of the castle were not reproduced).
On the other hand, the model created in a lost mold, printed via the “Fused Deposition Modeling (FDM)” process, was conclusive. The destruction of the mold was easy, and the geometric details of the model were preserved. To meet the specifications of “outdoor stored models” and “durable models,” construction materials were tested, and one was chosen.
To conclude, the chosen manufacturing path (molds created in 3D printing and casting of a construction material) meets all the criteria of the project’s specifications:
- Outdoor endurance and durability of the model: the chosen material, derived from construction, is specifically designed to withstand outdoor conditions while having a long lifespan;
- Good resolution: thanks to the resolution of the molds obtained by the “Fused Filament Manufacturing” process, the models obtained make the geometric details of the castles visible;
- Large size: the machines related to the “Fused Filament Fabrication” process are large;
- Low costs: the costs incurred by this manufacturing path were calculated and correspond to the values sought at the beginning of the project.
SETTING UP THE MANUFACTURING PATH IN A LARGE-SCALE MODEL
To set up the chosen manufacturing path, the issues presented below had to be resolved:
- Creation of a digital chain allowing, step by step, to go from a digital model to a large-scale model;
- Adaptation of the “theoretical” model of the castle (as existing at the time) to a realistic model taking into account the constraints of the manufacturing process;
- Setting of the 3D printed molds (layer thickness, pattern and filling density, etc.);
- Optimal formulation of the material constituting the model to optimize its mechanical properties and pourability;
- Implementation of a recycling process for 3D printed molds destroyed during demolding.
For this purpose, several test models were created: creation of octagonal towers, creation of the complete Guildo castle at a reduced scale, creation of a section of the Guildo castle at scale 1.

Models created to develop the setting of the manufacturing path
Thanks to these achievements, the optimal parameters and the digital chain of the manufacturing path were determined. This made it possible to create the large-scale demonstrator of the project. Although many improvements remain possible, this result proves that the large-scale model manufacturing path is functional and economically viable. The model is expected to be installed on the Guildo castle site during the year 2024!
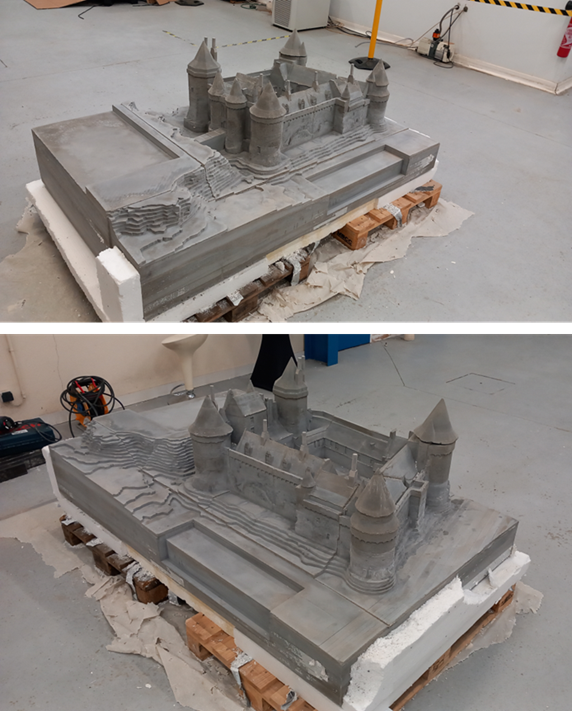
Large-scale project demonstrator
The project’s objectives were achieved; the project data, transferred to the Smart company by the SUNI-pft platform, will enable it to create new strongholds models in the future.
Are you fascinated by historical heritage and modern technology?